We build custom steel solutions for fixed and mobile equipment across the intermountain region

Equipment repair & rebuild
- We provide on-site visits from certified professionals as needed.
- We craft custom steel solutions that make your equipment last longer.
- We help you save money on long-term maintenance and repair.
- We price everything up front.
- We reverse-engineer repairs designed from original OEM parts.

Client Testimonials

“This is one of the best-run steel fabrication businesses in the western states! Very impressed with the operation and their ability to get things done.”
JK, SOS IT Services

Mobile equipment
- Truck liners
- Shovels
- Loader buckets
- Cutting edges

Fixed equipment
- Chute liners
- Conveying
- Drag chain flighting
- Grappling hooks
- Shaker screens
- Shredders
- Shredding screens

Call – Assess – Bid – Review – Fix


Call us for a consultation

We’ll Assess the
situation, create
drawings, take
photos, visit and
gather
information


We’ll submit
a Bid

We’ll Review it
with you and
your team


We’ll Fix the
problem
Call – Assess – Bid – Review – Fix
Our features
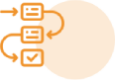
Custom Drawings

Our own delivery trucks
Get Your Solution Here
Got steel problems?
Shovel Story
We often replace the steel components in the big shovels that haul dirt for mines when the metal parts wear out. One time, someone parked a Komatsu shovel too close to a wall and it collapsed. It took out the safety cage on one side and caused a total equipment shutdown. We sent one of our guys over right away to measure the shovel and made a new one with harder steel. When that part finally wore out, we pulled up the specs we marked down the first time and made it all over again – with some measurement adjustments from the customer. Every time we rebuild a shovel, it’s a custom job because no two parts are ever alike.
Scrap Shredder Story
We get hired by recycling companies to replace and repair their shredding screens inside their scrap shredders all the time. One company hired us to fix a screen where the blades wore a hole clean through it. In order to get the scraps the right size, they had to run everything through the machine at least twice. But when they asked for a quote for a new screen from the manufacturer, they said it would take 20 weeks. We got it done in one. And, by using tougher metal, we extended the screen life by about 30%. After they knew there was a local company that could do a quicker, better job, they started coming to us a lot.